情報技術
圧接溶接の徹底解説
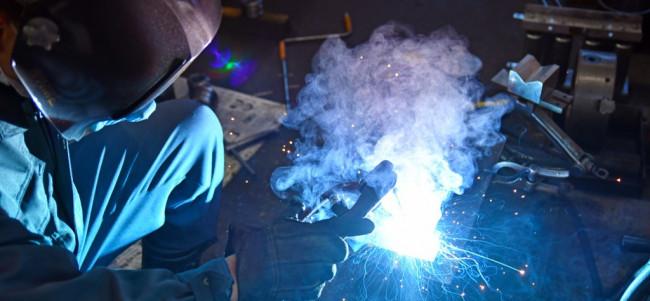
圧接(あっせつ)とは、接合する材料に圧力をかけ、材料表面を密着させることで、材料を接合する溶接法の一つです。圧接では、主に圧力が接合を促進する要素となり、材料が部分的に変形して結合する仕組みです。
この方法では、溶融溶接とは異なり、フィラー材(溶接金属)が不要で、材料自体が直接結びつくため、精密かつ高強度な接合が可能です。圧接は主に金属材料に対して使用されることが多く、接合強度が高く、材料の変形が少ないことから、産業界で広く利用されています。
圧接溶接の基本的な概念
接合する材料同士を圧力で押し付け、接合面を密着させることで、分子レベルでの接合が起こります。材料が圧力を受けると、表面の不純物や酸化膜が取り除かれ、材料の純粋な部分が露出します。この密着により、分子同士が相互作用して接合が形成されます。
圧接では、接合部を加熱する場合もあります。例えば、抵抗溶接や摩擦圧接では、熱を利用して接合部を軟化させ、圧力を加えることで接合します。熱が加わることで、材料の可塑性が高まり、より強固な接合が可能になります。
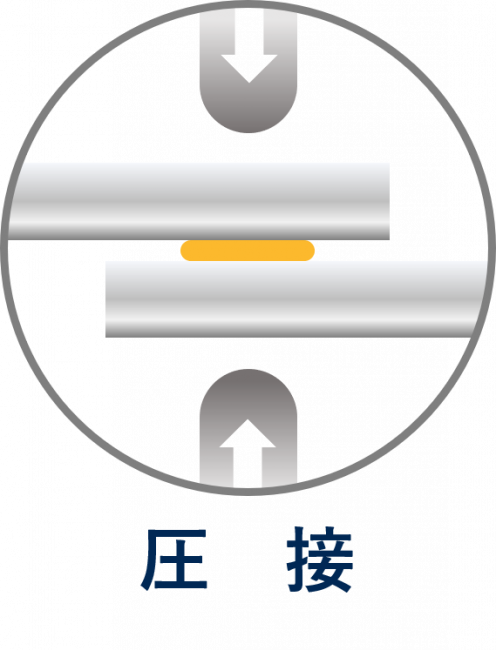
圧接溶接のメリット
圧接は、接合する材料に圧力を加えて密着させ、接合する技術で、溶融を伴わずに接合を行うため、特定の産業や用途で重宝されています。圧接は高い強度を持つ接合が可能であり、さまざまな材料に適用できる点から、多岐にわたる分野で活用されています。
圧接溶接のメリット① 高い接合強度
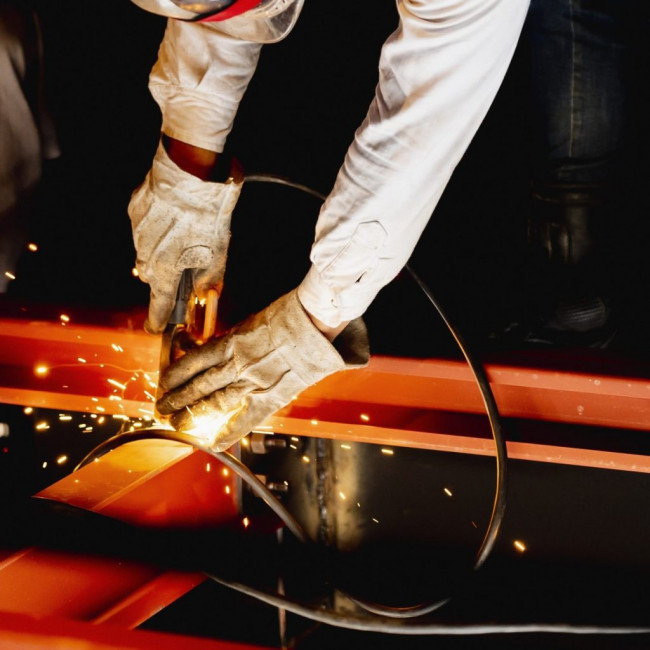
圧接の最大のメリットの一つは、高い接合強度が得られる点です。圧接では、材料の表面を密着させ、材料内部で分子レベルでの接合が行われます。加圧と加熱を組み合わせることで、材料が部分的に軟化し、凹凸が埋められて接合面が密着するため、接合部の強度が非常に高くなります。
特に摩擦圧接や抵抗溶接では、局所的に高温となり、材料が一時的に柔らかくなることで、接合が確実かつ強固に行われます。この結果、溶接後の接合部分は母材と同等、あるいはそれ以上の強度を持つことが多いです。
自動車産業などでは、この接合強度を活かして車体の主要部分を接合するためにスポット溶接(抵抗溶接の一種)が使用されています。ここでは、接合後の部品に強い衝撃や負荷がかかることを想定しており、圧接がその要求に応えています。
圧接溶接のメリット② 熱による変形が少ない
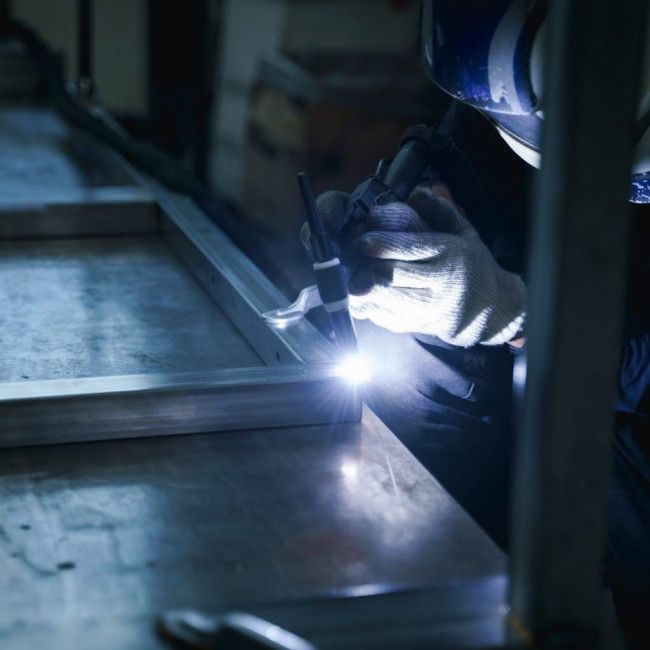
圧接は溶融を伴わないため、熱による変形や応力が少ないことも大きなメリットです。溶融溶接では、材料を高温で溶かし、それが固まる際に冷却速度の違いによるひずみや歪みが発生することがありますが、圧接ではこれが問題になりにくいです。
特に精密な部品や、形状変化が許容されない部品では、圧接の「低変形性」は非常に有効です。例えば、電子機器の製造では超音波圧接がよく使用されます。超音波圧接は、部品の表面を局所的に加熱して圧力をかけるため、熱影響部が極めて小さく、材料全体の熱変形がほとんどありません。このため、電子部品などの精密接合に適しています。
圧接溶接のメリット③ 異種材料の接合が可能
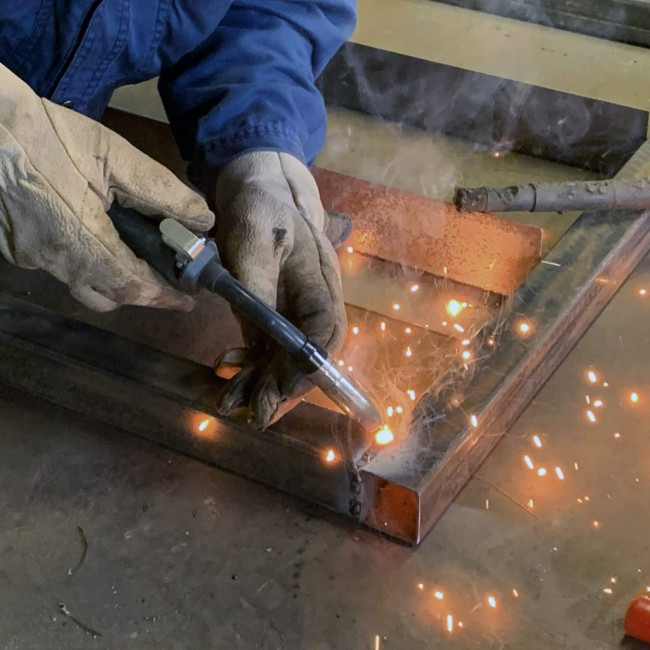
圧接のもう一つの大きな利点は、異種材料の接合が可能である点です。通常、溶融溶接では異種金属や材料を接合すると、溶接時に生じる化学反応や溶接金属の不均一な凝固が原因で、脆弱な接合となることが多いです。しかし、圧接では溶融が伴わないため、異種材料同士を高品質に接合することができます。
たとえば、摩擦圧接では、異なる金属や合金を接合する場合でも、熱による影響が限られているため、材料の特性を保ちながら接合が可能です。これにより、構造の軽量化やコストダウンが求められる産業(航空宇宙産業など)で非常に効果的です。
また、超音波圧接は、金属同士だけでなく、金属とプラスチックなど異なる性質を持つ材料同士を接合できるというユニークな特徴があります。これにより、電子部品やセンサーの製造など、精密機器における複合材料の接合にも活用されています。
圧接溶接のデメリット
圧接(あっせつ)は、材料に圧力をかけて接合する方法としてさまざまな産業で利用されていますが、いくつかのデメリットや制約も存在します。圧接のメリットは非常に多いものの、特定の条件や用途によっては制限が生じる場合があり、これらのデメリットを理解することが重要です。以下では、圧接のデメリットについて詳しく解説します。
圧接溶接のデメリット① 高価な設備が必要
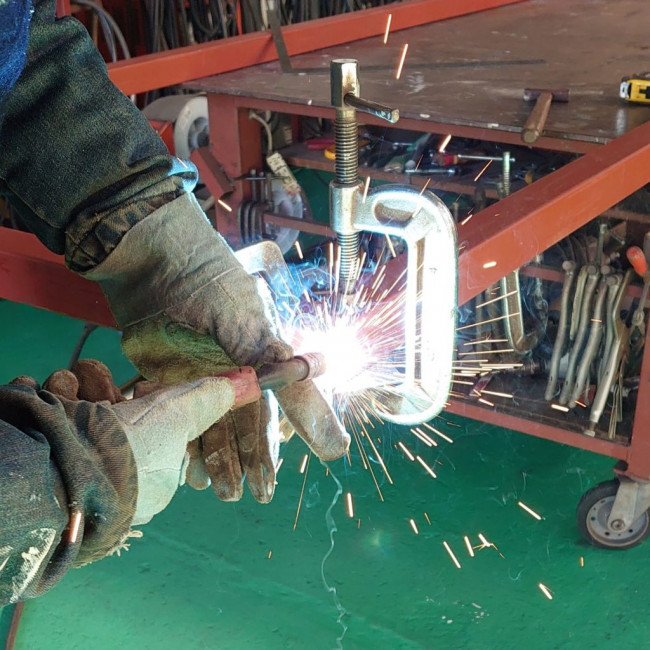
圧接では、接合に高い圧力を加えるための設備が必要です。例えば、抵抗溶接や摩擦圧接では、大きな圧力をかけるための専用の機械が必要となります。これらの機械や装置は非常に高価であり、初期投資が大きくなるという問題があります。また、圧接に使用される機械は通常、精密な圧力制御や温度管理が可能な装置であるため、運用コストやメンテナンスコストも高くなる傾向にあります。
特に、摩擦圧接や抵抗溶接に使用する機械は大規模であり、大量生産ラインや大型部品の接合には向いているものの、小規模な作業やプロトタイプ製造には適さない場合があります。このため、設備投資の費用がかさむことが圧接の大きなデメリットの一つと言えます。
圧接溶接のデメリット② 大型の部品や複雑な形状の接合が難しい
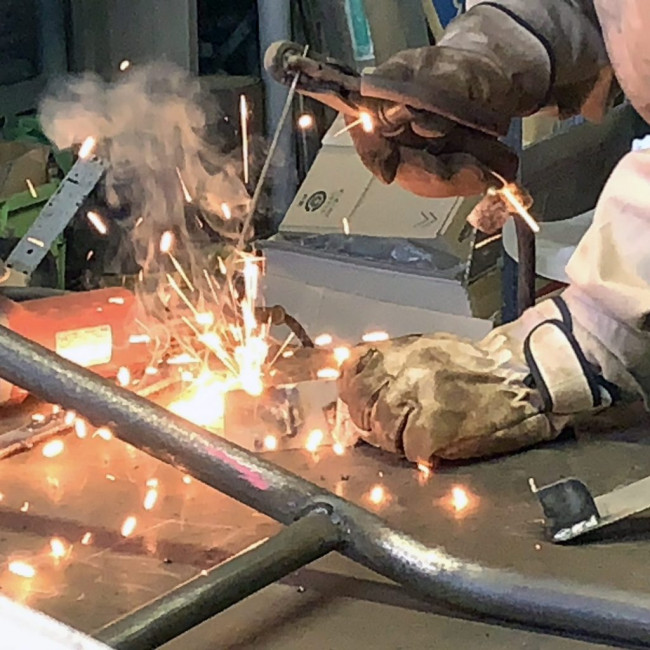
圧接は、接合面に圧力を均等に加える必要があるため、大型の部品や複雑な形状の部品を接合する際には制約が生じます。特に、接合面が均一でない場合や、接合部分が深く入り込んだ場所にある場合、圧力を効果的に加えることが難しくなります。
例えば、抵抗溶接では、電極を直接接合面に押し当てることで圧力と電流を供給しますが、電極が届かない複雑な形状の部品では接合が難しくなります。また、大型部品では、全体に均一な圧力をかけることが困難であり、その結果、接合不良や局所的な強度不足が発生することがあります。
これにより、圧接は平坦な表面や比較的小さな部品の接合には適しているものの、大規模な構造物や複雑な幾何学的形状を持つ部品には向いていない場合があると言えます。
圧接溶接のデメリット③ 材料表面の準備が重要
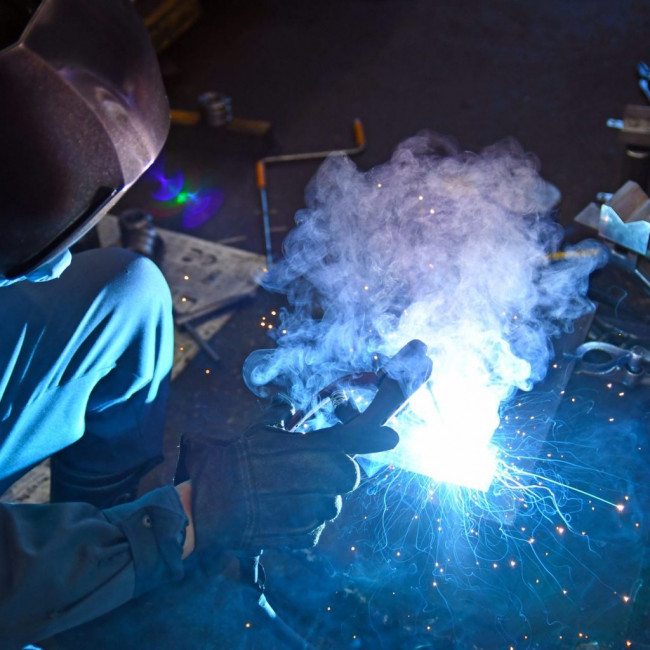
圧接では、接合する材料の表面が清潔かつ平滑であることが非常に重要です。材料表面に酸化膜、油、汚れ、不純物などが存在すると、接合の質が大きく低下します。これらの不純物が接合面に残っていると、材料同士が十分に密着できず、接合強度が低下したり、接合が完全に行われない可能性があります。
そのため、圧接を行う前に、材料表面の清掃や酸化膜の除去が必要となる場合が多いです。例えば、摩擦圧接では、接合面が摩擦熱で清掃されることが多いですが、超音波圧接や冷間圧接では、事前にしっかりとした表面準備が求められます。このような前処理が必要なため、作業工程が複雑化し、時間と労力がかかることがあります。
圧接と溶接プロセスの種類
抵抗溶接(スポット溶接、シーム溶接)
概要 | 電流で加熱し圧力を加え、抵抗熱で材料が軟化しすることで接合 |
---|---|
特徴 | 量産向き。部材変形が少なく、外観が綺麗に仕上がる |
摩擦圧接
概要 | 片方を高速回転、もう片方を圧力をかけながら回転させ、摩擦熱で接合 |
---|---|
特徴 | 材料変形が少なく、頑丈な接合。異種材料の接合にも適している |
突合せ圧接(バット溶接)
概要 | 接合する部材の端部同士を直接圧力で押しつける方法 |
---|---|
特徴 | 高強度で継ぎ目が滑らか。導電性や流体の流れが良好な接合が得られる |
超音波圧接
概要 | 高周波の超音波振動を用いて、接合面に局所的な摩擦熱で接合 |
---|---|
特徴 | 熱による影響が少ないため、材料の物性を保持できます |
圧接過程の物理的メカニズム
圧接の過程は、材料を加圧することで接合するプロセスであり、物理的には複数の要因が絡み合って進行します。この過程では、接合する材料の表面が密着し、分子レベルでの接合が起こるため、接合部の強度が母材と同等かそれ以上になります。圧接の物理的メカニズムは、接合する材料の変形、表面の清浄化、熱の発生と伝導、そして分子レベルでの結合などが主な要素です。ここでは、これらの各要素について詳しく説明します。
塑性変形
圧接の最も基本的なメカニズムの一つは、材料に圧力を加えることで生じる塑性変形です。塑性変形とは、材料に力を加えたとき、その材料が元の形状に戻らずに変形したままになる現象です。圧接の際には、接合面に対して圧力を加えることで、材料表面が変形し、互いに接触していなかった微細な凹凸が埋まり、密着することが促進されます。
たとえば、摩擦圧接では、接合する材料を回転させながら圧力を加えることで、摩擦熱が発生し、材料表面が一時的に軟化します。軟化した材料が塑性変形を起こすことで、接合面の凹凸が埋まり、均一で密着した接合が実現されます。これにより、接合面が広がり、強固な結合が得られます。
接触表面の清浄化
圧接では、接合する材料の表面が清浄であることが非常に重要です。接合面に汚れ、酸化膜、油、不純物などが存在すると、材料同士が十分に密着できず、接合強度が低下する可能性があります。そのため、圧接過程では表面の清浄化が行われることが多く、これには物理的または化学的な作用が関与します。
たとえば、摩擦圧接では、接合面が回転によって擦り合わされることで摩擦熱が発生し、その熱によって表面の酸化膜や不純物が除去されます。これにより、純粋な金属表面同士が接触しやすくなり、強力な接合が可能になります。同様に、超音波圧接では、超音波振動が材料表面に振動エネルギーを与え、表面の汚れや酸化膜が破壊されて清浄化されるプロセスが進行します。
原子間の拡散
圧接の接合メカニズムの一部は、接合面での原子間の拡散に基づいています。圧力を加えて接合する材料同士を密着させると、接触した部分で材料の原子同士が拡散し始めます。この拡散プロセスは、特に高温環境で促進され、接合面の原子が互いに入り込んで混ざり合うことで、材料同士が強固に結合します。
たとえば、圧力溶接の一種である抵抗溶接では、接合面に通電して発生する抵抗熱によって材料が局所的に高温となり、原子が活発に拡散します。これにより、接合面に強固な原子結合が形成され、母材と同等の強度を持つ接合部が生まれます。
原子拡散の速さや範囲は、温度や材料の特性に依存します。高温で行われる圧接プロセス(例えば摩擦圧接や抵抗溶接)では、材料内部の原子が活発に移動し、接合面が強固に結合されます。
局所的な加熱と冷却
圧接の多くのプロセスでは、材料に圧力を加えるだけでなく、局所的な加熱も行われます。この加熱は、材料の塑性変形を促進し、接合面での密着をより強固にする役割を果たします。例えば、摩擦圧接では、材料同士を高速で回転させながら押し付けることで摩擦熱が発生し、その熱によって材料が軟化します。軟化した材料はより簡単に塑性変形を起こし、接合面が広がります。
また、抵抗溶接では、接合面に通電することで材料が加熱されます。電流が流れると接合面に電気抵抗が生じ、それが熱エネルギーに変換されます。この局所的な加熱によって材料が軟化し、加圧による接合が促進されます。その後、加圧された状態で冷却が進むと、材料は固化し、強固な接合が得られます。
このような局所的な加熱と冷却のサイクルは、圧接の過程において非常に重要です。加熱によって材料が軟化し、接合しやすくなる一方で、冷却によって接合が固定され、強固な接合部が形成されます。
機械的振動の影響(超音波圧接の場合)
超音波圧接は、他の圧接方法とは異なる特異なメカニズムを持っています。このプロセスでは、機械的な振動が接合面にエネルギーを供給し、接合を促進します。具体的には、20kHz以上の高周波数の超音波振動が材料に与えられ、接合面での微小な摩擦が発生します。
この摩擦は、材料表面の汚れや酸化膜を除去し、純粋な金属同士が接触する機会を増やします。また、超音波による局所的な加熱も発生し、材料が柔らかくなるため、接合がさらに促進されます。超音波圧接は、比較的低温で行われ、熱影響が少ないため、熱に敏感な材料や精密な電子部品の接合に適しています。
圧力と時間の関係
圧接の成功には、圧力と時間のバランスが重要です。接合面に対して適切な圧力を加え続けることで、材料が所望の形状に塑性変形し、接合面が十分に密着することが可能になります。しかし、圧力が不足すると、接合が不十分になり、逆に過剰な圧力をかけすぎると、材料が破損したり変形しすぎる可能性があります。
さらに、圧接プロセスには一定の時間が必要です。圧力を加えてから材料が十分に変形し、分子間結合が形成されるまでには時間がかかります。このため、圧接には「保持時間」が設定されることが多く、適切な圧力で材料を一定期間加圧し続けることが重要です。
圧接溶接の応用分野
圧接溶接は、溶融溶接とは異なり、接合面を溶かさずに材料を接合するため、多様な産業や応用分野で活用されています。以下では、圧接溶接が特に有効な主な応用分野を紹介します。
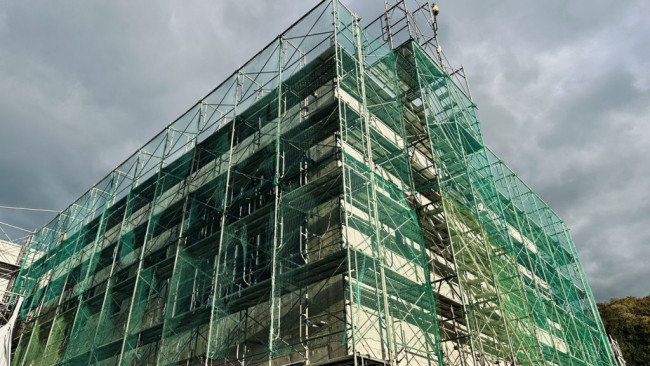
建設業
圧力溶接は、鉄筋や配管の接合に広く利用され、特に異種材料や異なる直径の鉄筋同士の接合において高い効率性を発揮します。鋼材同士の接合においても、熱影響が少ないため、母材の特性を保ちながら強固な接合が実現します。抵抗溶接は、ビルや橋梁の鋼構造物に使用され、迅速かつ信頼性の高い接合を提供します。
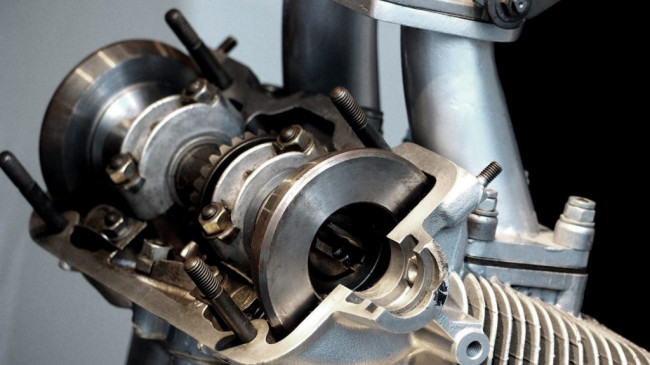
自動車産業
摩擦圧接は、エンジンのシャフトや駆動系部品、ギアや車軸の接合に利用されます。異種金属の接合にも適しており、特定の機械的特性が求められる部品に対して有効です。また、抵抗溶接は、自動車の車体フレームやドア、マフラーなどの部品接合に用いられます。特に、自動車の構造的な部分では、スチールやアルミニウム部品の接合に広く使用されています。
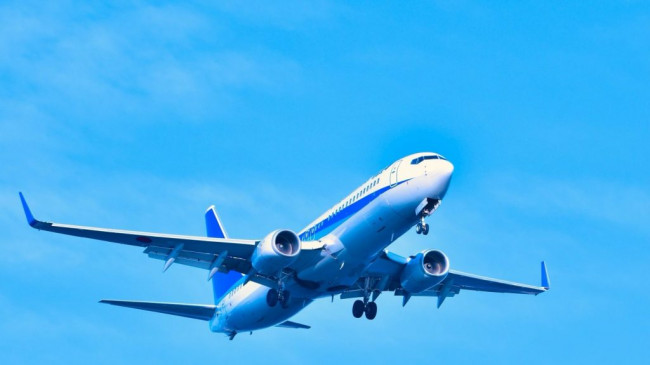
航空宇宙産業
摩擦圧接は、飛行機のタービンブレード、燃料タンク、エンジンコンポーネントなどの重要な部品の製造に利用されます。これらの部品は、極端な温度や圧力にさらされるため、高い接合強度が不可欠です。超音波圧接は、航空宇宙で使われる複合材料や、軽量なアルミニウム・チタンなどの金属部品の接合に適しています。特に、配線や電子機器の接続部分に多く使われています。