情報技術
スポット溶接とは
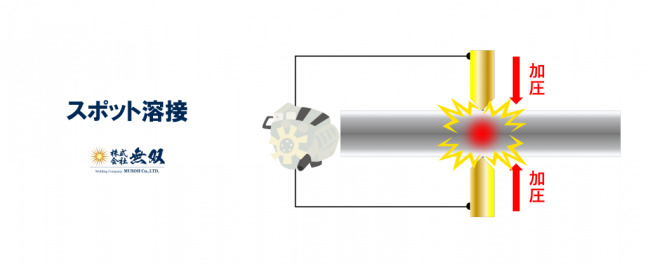
スポット溶接(スポットようせつ)は、金属の接合方法の中でも特に広く利用されている抵抗溶接の一種です。この方法では、2枚以上の金属板を重ね、その接合部に電極を挟み込んで電流を流し、発生する熱で局所的に溶融させて接合します。加熱による接合は短時間で行われるため、非常に効率的です。また、接合部が小さな点状になることから「スポット溶接」という名称が付けられています。
スポット溶接とは
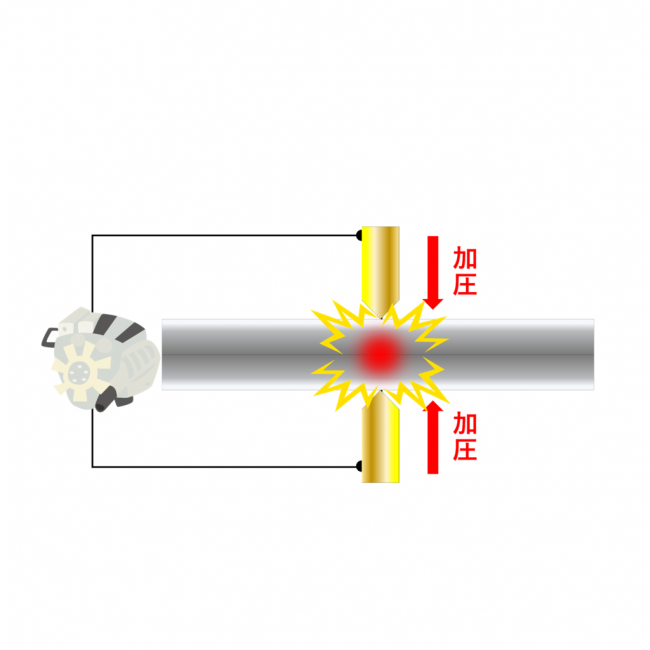
スポット溶接は、効率的でコスト効果が高い一方、適切な溶接条件の設定や材料の選定が求められるため、専門知識と経験が必要です。基本的な仕組みとしては、電極を通じて金属接合部に圧力を加えながら高電流を短時間流し、局所的な発熱を利用して金属を溶融させます。その後、冷却することで固化し、接合が完成します。
スポット溶接はそのシンプルな仕組みから、一見すると誰でも簡単に扱えるように見えますが、実際には多くの要因が溶接品質に影響を与えます。たとえば、電極の材質や形状、溶接に使用する電流や通電時間、さらには金属板の表面状態が接合強度を左右します。そのため、スポット溶接を成功させるには基礎知識と技術力が不可欠です。
スポット溶接の種類
スポット溶接にはいくつかの種類があり、用途や目的に応じて使い分けられます。以下では、それぞれの特徴と主な利用分野について詳しく解説します。
抵抗スポット溶接
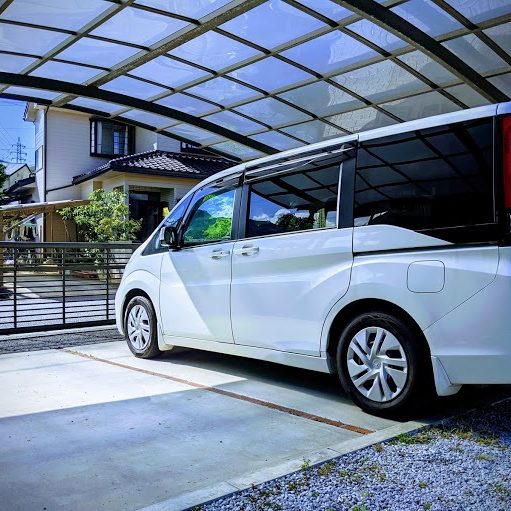
抵抗スポット溶接は、最も一般的なスポット溶接の形式です。電極を通じて金属板に高電流を流し、電流が接触抵抗によって熱エネルギーに変換される仕組みを利用しています。この方法は、比較的薄い金属板を接合するのに適しています。主に以下のような特徴があります。
適用範囲 | 鉄鋼やステンレス鋼などの導電性の高い金属 |
---|---|
メリット | 操作が簡単で、自動化が容易 |
デメリット | 厚い金属板や異種金属の接合には向かない |
自動車産業では、この方法が車体パネルの組み立てで多用されています。
プロジェクション溶接
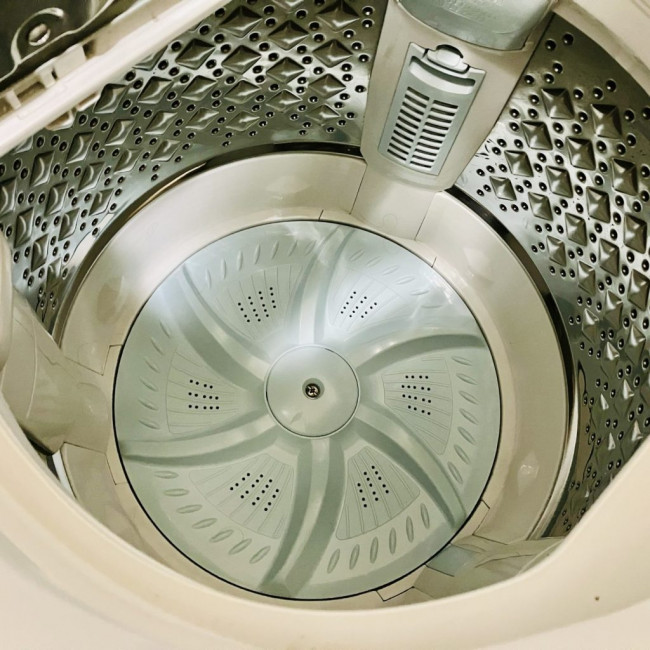
プロジェクション溶接は、金属部材に事前に突起(プロジェクション)を形成しておき、その突起部を溶接する方法です。この方式では、電流と圧力が突起部分に集中するため、効率的にエネルギーを使用できます。以下のような特徴があります。
適用範囲 | 複数の金属部材を一度に接合する場合に有効 |
---|---|
メリット | 接合点を事前に制御でき、溶接品質が安定 |
デメリット | 突起形成の追加工程が必要 |
家電製品や電気部品の製造でよく見られます。
突合せスポット溶接
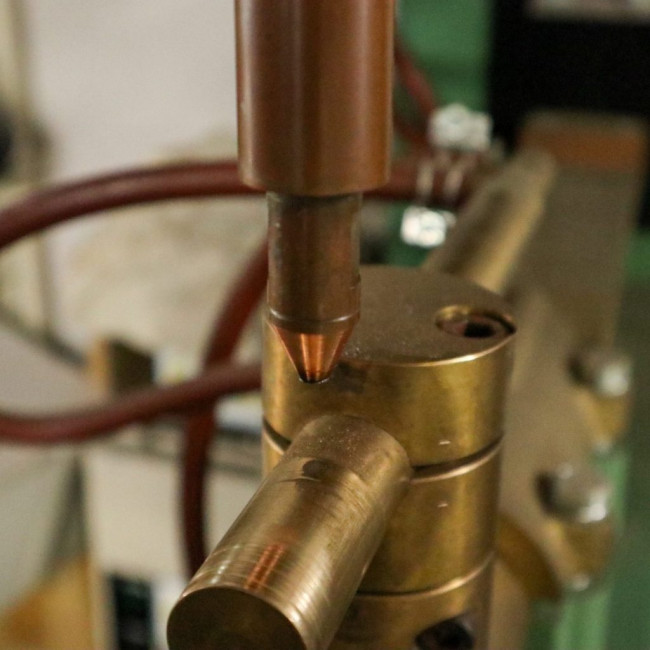
突合せスポット溶接は、金属部材の端面を接合するための方法です。この方法は主に線材や円筒状部材の接合に用いられ、以下の特徴があります。
適用範囲 | ワイヤやパイプ、円筒状の部材 |
---|---|
メリット | 高い接合強度を実現 |
デメリット | 溶接設備がやや特殊 |
スポット溶接の手順
スポット溶接のプロセスは以下の段階に分かれています。それぞれの工程での正確さが、最終的な接合品質に大きく影響します。
スポット溶接のステップ1
溶接面の準備
スポット溶接の工程は、まず接合する金属板の表面準備から始まります。金属板の表面には、酸化膜、油分、ほこり、その他の異物が付着している場合が多く、これらが溶接品質に直接影響を与えます。汚れや不純物が残った状態では、電流が均一に流れず、接合部の強度が低下したり、不完全な溶接が生じたりすることがあります。そのため、接合面は完全に清掃する必要があります。
スポット溶接のステップ2
電極の設置
準備が完了した金属板は、次に溶接機の電極の間にセットされます。電極は、接合部に対して適切な圧力を加えるだけでなく、通電のための役割も担っています。電極の設置位置がずれていたり、接触が不均一だったりすると、通電時のエネルギー分布が偏り、接合部に不良が生じる可能性があります。そのため、電極を正確に配置することが求められます。
スポット溶接のステップ3
通電と加熱
電極の設置が完了したら、いよいよ通電工程に入ります。この段階では、高電流が短時間にわたって流され、接合部が局所的に加熱されます。通電時には、金属板間の接触抵抗によって発熱が生じ、金属が溶融状態に達します。この溶融が、スポット溶接の核心的な部分です。
スポット溶接のステップ4
冷却と圧力保持
通電が完了すると、金属板の接合部は溶融状態から固化へと移行します。この段階では、電極で圧力を維持しながら冷却が行われます。冷却により、溶融した金属が再び結晶化し、強固な接合が形成されます。圧力を保持することは、接合部の均一性を確保し、内部に気泡や亀裂が発生するのを防ぐために不可欠です。
この冷却と圧力保持の工程を丁寧に行うことで、接合部は高い強度と耐久性を持つようになります。最終的な品質がここで決まると言っても過言ではありません。
スポット溶接のメリットとデメリット
スポット溶接のメリット
短時間で接合 | 非常に短時間で接合が可能で量産向き |
---|---|
自動化が容易 | 自動化が可能な為、生産ラインに組み込むことが簡単 |
高い接合強度 | 金属溶融のため、接合部は非常に強固で高耐久性 |
材料の無駄が少ない | 他溶接に比べ、追加材料を必要としません |
ティグ溶接のデメリット
材質の制約 | 主に導電性が良い金属で、プラスチックや異種材料は不可 |
---|---|
サイズ制限 | スポット溶接の接合範囲は、電極のサイズに依存。大きな接合部には不可 |
初期コスト | 溶接機や電源装置の導入に多額のコスト |
検査が困難 | 内部構造不良が目視確認しにくく、検査技術が必要になる場合がある |
スポット溶接の応用例
ティグ溶接は、以下のような産業や場面で幅広く利用されています。
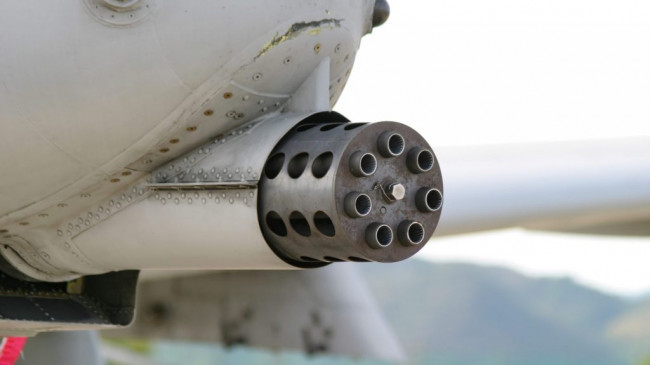
航空機産業
航空機やロケットなどの製造においては、軽量化と高強度が特に重要です。この分野でもスポット溶接が活用されています。例えば、航空機の外板や内部構造、ロケットのタンクなどは、スポット溶接による接合が行われています。
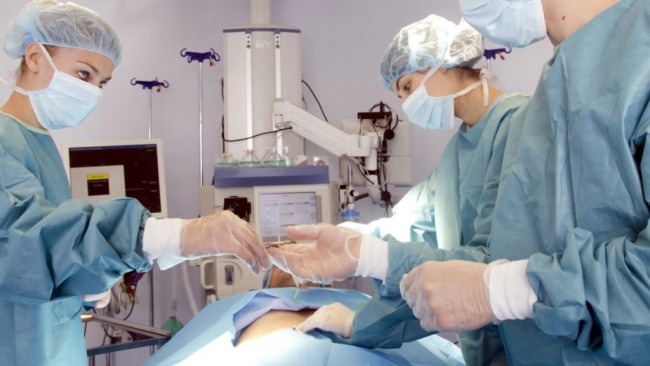
医療機器製造
医療機器の製造では、高精度かつ高品質な接合が求められます。たとえば、手術器具や医療用デバイスの金属部分の接合にスポット溶接が使用されています。特に、不純物が残らず、接合部分が滑らかで衛生的な仕上がりになる点が医療分野で評価されています。
.jpg)
自動車産業
スポット溶接は、自動車製造における欠かせない技術です。特に車体のフレームやボディパネルの接合には、スポット溶接が多用されています。自動車は軽量化と強度のバランスが求められる製品であり、スポット溶接の局所的かつ強固な接合がこの要求に応えています。
スポット溶接の必要条件と注意点
スポット溶接の必要条件
1.電極の適切な選定
電極の材質や形状は、接合する金属や溶接条件に応じて選ぶ必要があります。
2.適正な溶接条件
電流値、通電時間、圧力の3要素を適切に設定することで、高品質な溶接が可能になります。
3.接合面の清潔さ
表面汚れや酸化物は通電効率を低下させるため、事前の清掃が必要です。
スポット溶接の注意点
1.火傷や感電のリスク
溶接中は高温や高電流を扱うため、安全管理が重要です。
2.熱による変形の管理
接合部の熱膨張や冷却収縮が変形を引き起こす可能性があるため、治具を使用して部材を固定する必要があります。
3.内部不良の検査
特に重要な構造物では、超音波探傷やX線検査などで内部欠陥を確認することが推奨されます。
溶接の加工実績

真空バルブのTIG溶接
融点3380℃と金属の中で最も高融点のタングステンまたはタングステン合金を電極とし使用
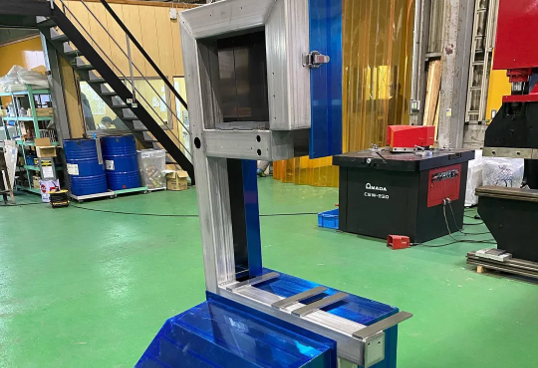
オールステンレス製の溶接
青のビニールテープの箇所はSUS430、それ以外の部分にはSUS304の複合製品です。
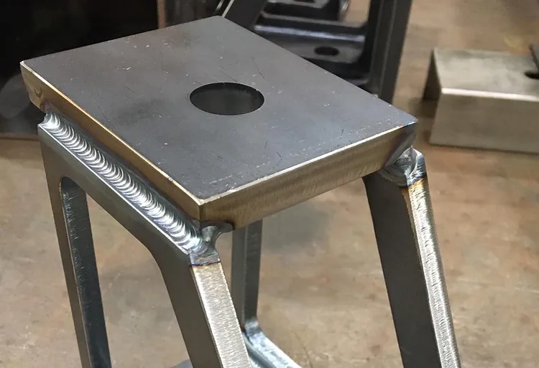
ブラケットのTIG溶接
溶接後の反り・歪みと角を溶かさないように気をつけ、ビードも綺麗に出ています。
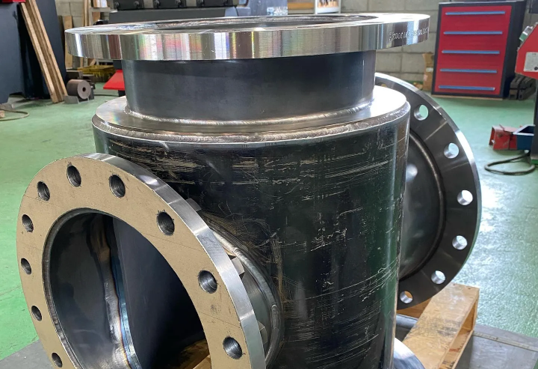
大型バルブのTIG溶接
ピンホールができないように注意を払うことがポイントです。
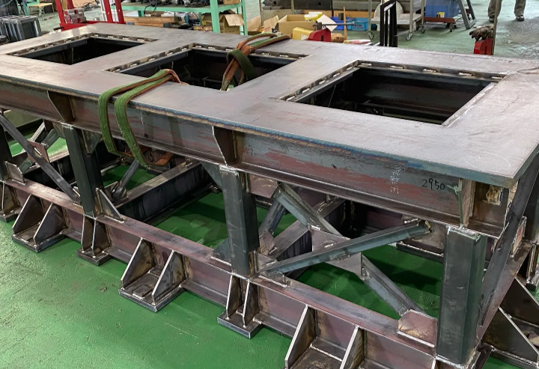
検査用架台の溶接
材料取りと溶接時の歪み、反りに注意しながらの取り付けに配慮。
.png)
ステンレスラックの溶接
スペースが限られる為、サイズを確認して寸法しました。