情報技術
ティグ溶接(TIG溶接)とは
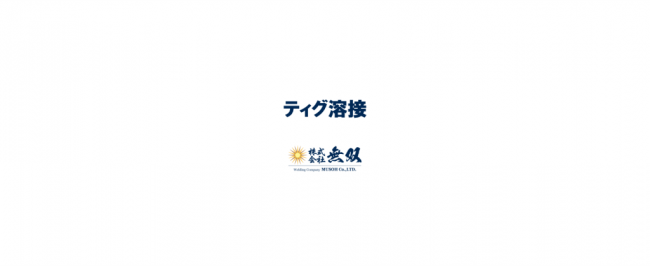
TIG(Tungsten Inert Gas)溶接は、タングステン電極と不活性ガスを使用して金属を接合する溶接方法で、高精度かつ高品質な仕上がりが求められる場面で使用されます。不活性ガス(主にアルゴンやヘリウム)がアークと溶接部を保護し、酸化や窒化を防ぐことで、接合部の物理的・化学的特性を損なわないことが最大の特徴です。この特性により、精密機器や重要な構造部品の製造で広く採用されています。
ティグ溶接とは
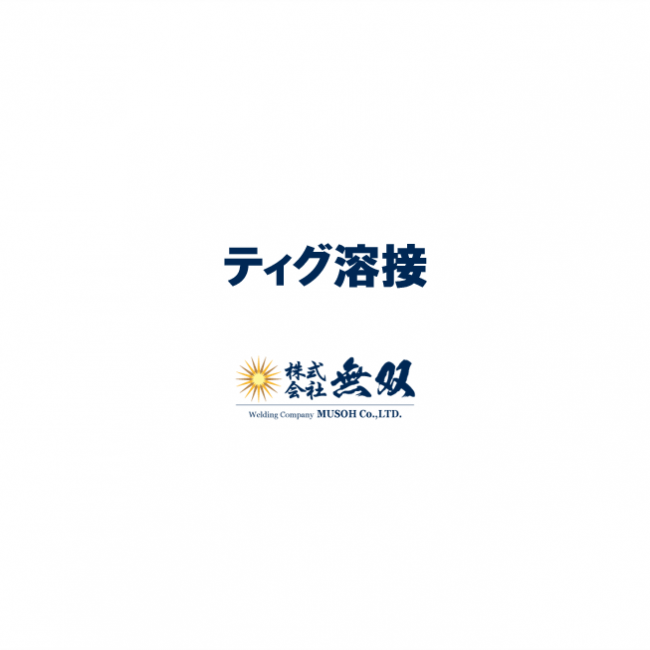
タングステン電極は非常に高い融点(約3,400℃)を持ち、溶融することなく安定したアークを形成します。この電極が母材に直接触れることなく、アークの熱によって母材を溶融し、必要に応じて溶加材を供給して接合が行われます。溶接部は非常にきれいな仕上がりとなり、後処理が最小限で済むことも大きな利点です。
TIG溶接は1930年代に開発され、当初は航空機産業でアルミニウムやマグネシウムの溶接を目的として使用されました。それ以前の溶接方法では酸化膜の影響で接合品質に限界がありましたが、不活性ガスを使用するTIG溶接の登場により、金属の特性を損なうことなく接合できるようになりました。現在では、自動車、建設、電子機器、医療機器など、幅広い分野で不可欠な技術となっています。
ティグ溶接の種類
TIG溶接には作業条件や金属の種類に応じていくつかの種類があり、それぞれの特徴に基づいて最適な方法を選択します。
直流TIG溶接
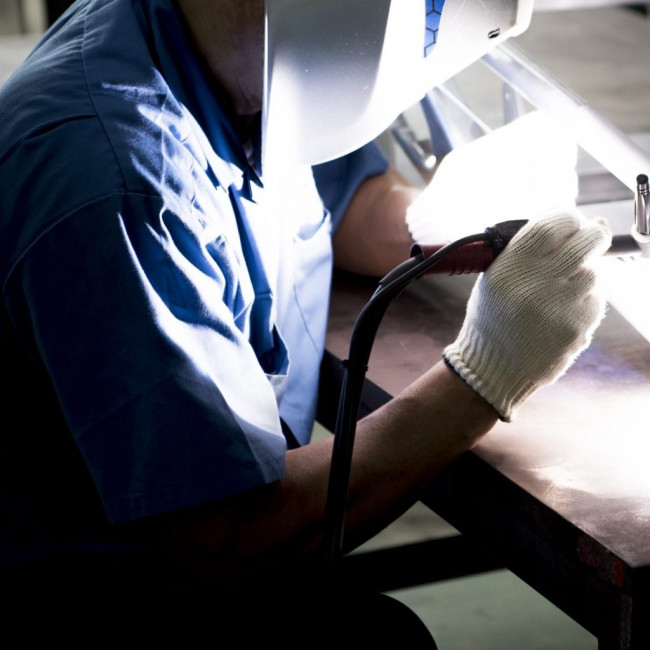
直流電流(DC)を用いた溶接で、主に鉄やステンレス鋼などの導電性の高い金属に適しています。直流の特性により、アークが安定しやすく、溶接部の熱集中が可能です。これにより、厚みのある金属や複雑な形状の部品でも効率的に溶接ができます。
使用金属例 | 鉄、ステンレス鋼、銅 |
---|---|
特徴 | 精密溶接かつ効率的作業が出来る |
交流TIG溶接
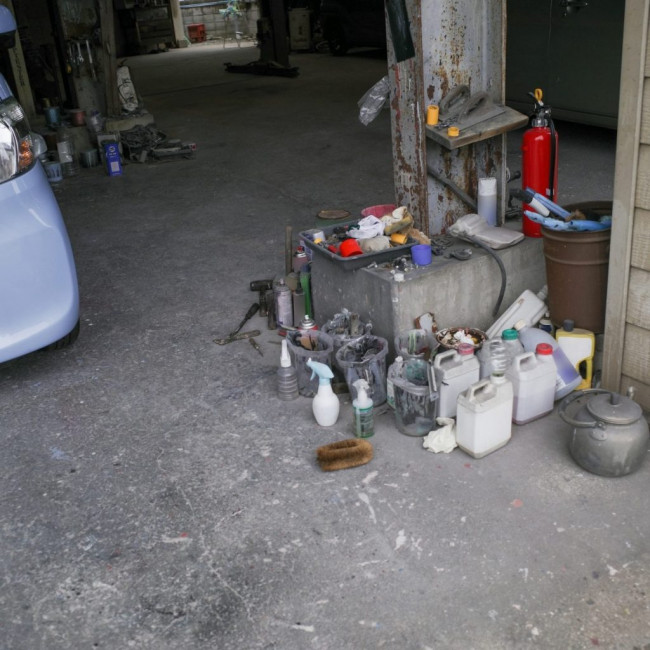
交流電流(AC)を用いるTIG溶接は、アルミニウムやマグネシウムの溶接に適しています。これらの金属は酸化膜を形成しやすく、この酸化膜が溶接品質を低下させる可能性があります。交流の正極では酸化膜が除去され、負極では熱が金属に集中することで、品質の高い接合が可能になります。
使用金属例 | アルミニウム、マグネシウム |
---|---|
特徴 | 酸化膜を効率的除去で高品質接合。 |
パルスTIG溶接
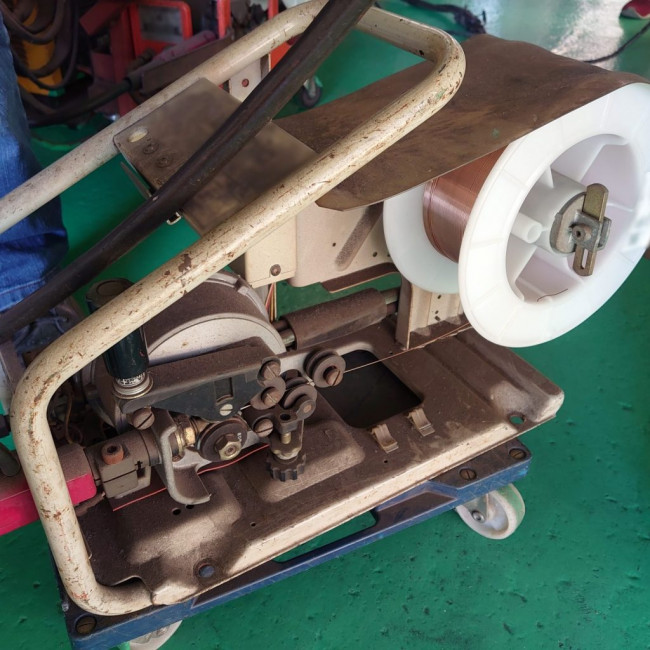
パルス電流を用いる溶接方法で、アークの熱を断続的に供給します。これにより、薄板や小型部品の溶接で熱による変形を最小限に抑えることができます。また、材料が薄い場合でも溶けすぎを防ぎ、均一で安定した接合を可能にします。
使用例 | 薄板の溶接、航空機や医療機器 |
---|---|
特徴 | 熱管理が容易で、歪みを抑えた溶接 |
ティグ溶接の手順
TIG溶接を成功させるには、正確な手順を守ることが重要です。
ティグ溶接のステップ1
溶接面の準備
溶接部の清掃は、TIG溶接の品質に直接影響を与えます。特にアルミニウムやステンレス鋼では、表面の汚れや酸化膜が溶接の妨げとなるため、溶接前に適切な処理が必要です。化学的な洗浄剤やサンドペーパーを使用して清掃し、表面を滑らかにします。
ティグ溶接のステップ2
電極と不活性ガスの選定
タングステン電極の種類(純タングステン、トリウムタングステン、セリウムタングステンなど)を適切に選びます。また、不活性ガスとしてアルゴンやヘリウムを使用します。アルゴンは一般的ですが、ヘリウムを加えるとアーク温度が高くなり、厚い金属の溶接に有効です。
ティグ溶接のステップ3
溶接機の設定
適切な電流や電圧を設定します。溶接対象の金属や作業環境に応じて設定を調整する必要があります。試験溶接を行い、条件が適切かを確認します。
ティグ溶接のステップ4
溶接の実施
タングステン電極と母材の間にアークを形成し、アークの熱で金属を溶融させます。溶加材が必要な場合、適切なタイミングで供給します。電極の角度やアークの距離を一定に保つことで、溶接部の均一性を確保します。
ティグ溶接のステップ5
冷却と仕上げ
溶接が完了したら、溶接部を自然に冷却します。必要に応じて、仕上げの研磨や防錆処理を行い、溶接部の見た目と耐久性を向上させます。
ティグ溶接のメリットとデメリット
ティグ溶接のメリット
高品質な仕上がり | 溶接部が酸化や窒化の影響を受けにくく、スラグがほとんど発生しない |
---|---|
広範な金属対応性 | 特に他の溶接方法では接合が難しい非鉄金属の溶接でその力を発揮する |
精密な制御が可能 | 薄板や複雑な形状の部品を溶接する際にも熱歪みを最小限に抑えられる |
溶加材の選択自由度 | 母材のみで接合する自溶溶接も可能で、溶接部の純度を高めたい場合や、美観重視の際に有用 |
ティグ溶接のデメリット
熟練技術が必要 | 特にアークの長さや溶加材の供給タイミングの適切な管理能力が必要 |
---|---|
設備コストが高い | TIG溶接機は他の溶接機に比べて高価であり、不活性ガスの供給装置も必要 |
溶接速度が遅い | アーク制御に時間がかかり、手動は他溶接に比べて速度が遅く、量生に不向き |
風に弱い | 不活性ガスがアークを保護する仕組み上、風の影響を受けやすく、屋外は難しい |
ティグ溶接の応用例
ティグ溶接は、以下のような産業や場面で幅広く利用されています。
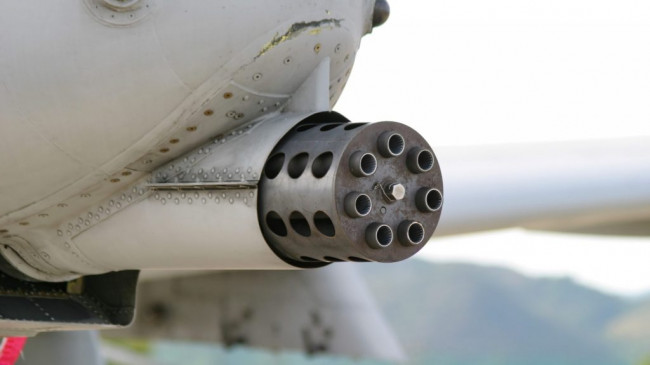
航空機産業
軽量で強度が求められるアルミニウムやチタン合金の溶接に使用されます。特に航空機の機体構造やエンジン部品では、高品質な溶接が必要不可欠です。TIG溶接の高精度な接合は、航空機の安全性や耐久性を向上させます。
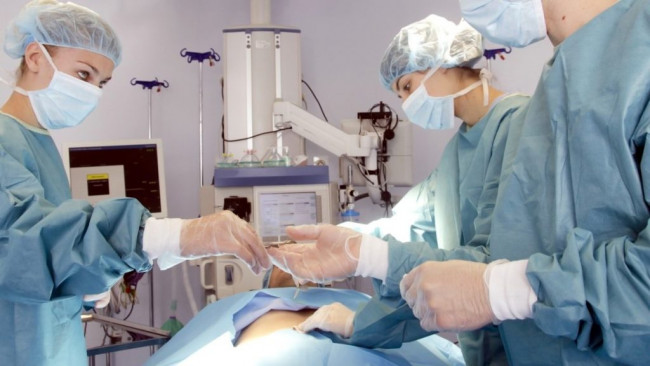
医療機器製造
医療用具や外科用器具では、接合部の衛生面や精度が重要です。TIG溶接はステンレス鋼やチタンを使用した高精度な部品製造に適しており、人工関節や手術器具の製造に欠かせない技術です。
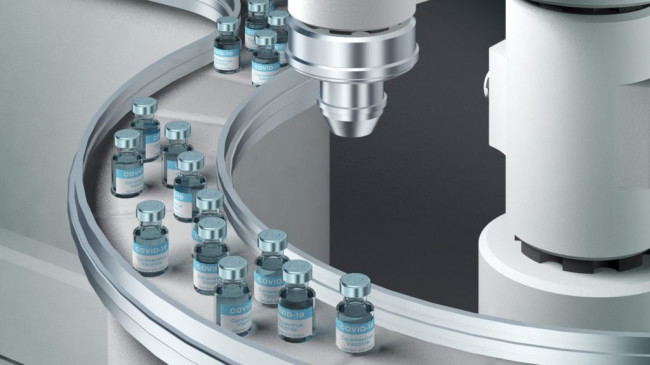
化学プラント
耐腐食性が求められる配管や容器の製造に使用されます。特に化学薬品に対して高い耐性を持つ金属(例:ステンレス鋼、チタン)の接合が可能で、長期間の信頼性を提供します。
ティグ溶接の必要条件と注意点
TIG溶接を実施する際には、以下の条件と注意点を守ることが重要です。
適切な設備と材料の選定
・溶接機の選定:DCまたはACの特性を理解し、金属に適した機械を選びます。
・不活性ガスの供給:アルゴンガスの純度が高いほど溶接品質が向上します。
作業環境の整備
・作業場所は風を防ぐ措置を取り、不活性ガスの流出を最小限に抑えます。
・十分な喚起を確保し、溶接ヒューム(煙)を吸引する装置を設置します。
技術的なトレーニング
溶接技術者は、適切なトレーニングを受け、タングステン電極の角度や溶加材の供給を的確に行う能力が求められます。
試験溶接の実施
本溶接の前に試験を行い、設定条件が適切かを確認します。特に重要な構造物では、非破壊検査で品質をチェックします。
溶接の加工実績

真空バルブのTIG溶接
融点3380℃と金属の中で最も高融点のタングステンまたはタングステン合金を電極とし使用
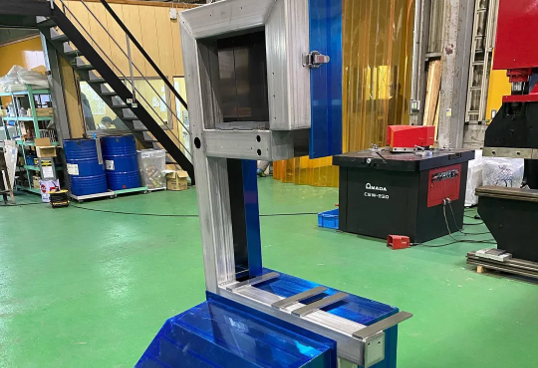
オールステンレス製の溶接
青のビニールテープの箇所はSUS430、それ以外の部分にはSUS304の複合製品です。
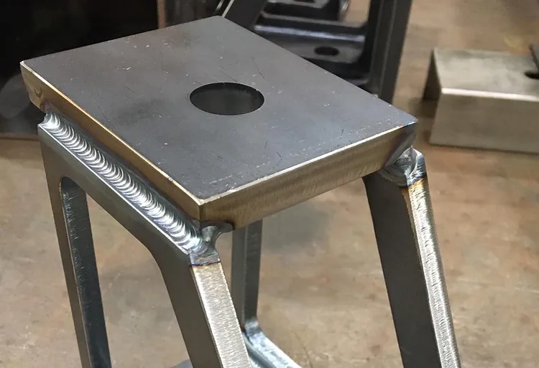
ブラケットのTIG溶接
溶接後の反り・歪みと角を溶かさないように気をつけ、ビードも綺麗に出ています。
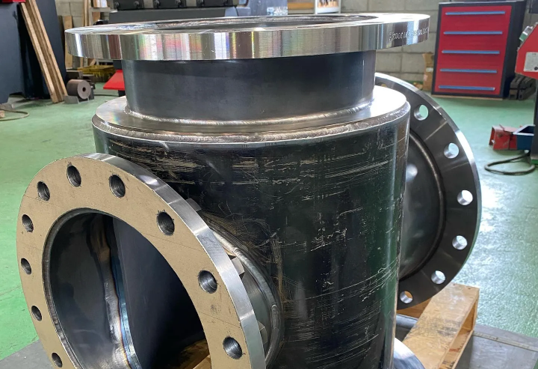
大型バルブのTIG溶接
ピンホールができないように注意を払うことがポイントです。
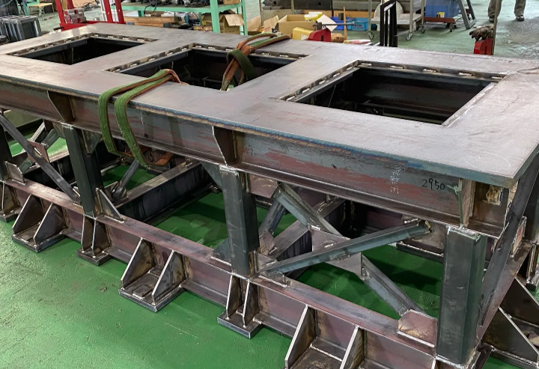
検査用架台の溶接
材料取りと溶接時の歪み、反りに注意しながらの取り付けに配慮。
.png)
ステンレスラックの溶接
スペースが限られる為、サイズを確認して寸法しました。